Table of Content
High-Performance Liquid Chromatography (HPLC) is a cornerstone analytical technique widely used in chemistry, biochemistry, and pharmaceuticals for separating, identifying, and quantifying components in complex mixtures. Its precision and versatility make it indispensable for quality control, drug development, environmental analysis, and many other fields. However, achieving consistent and accurate results with HPLC is not without challenges. Even minor deviations in system performance can significantly impact the quality of data, leading to time-consuming troubleshooting and potential delays in research or production timelines.
This article aims to address the most frequently encountered issues in HPLC operation. For each problem, we will provide a detailed analysis of the underlying causes and offer practical solutions to help users optimize their HPLC systems and maintain reliable results.
Abnormal Pressure
Pressure anomalies are among the most frequently encountered challenges in HPLC operation. These issues can significantly disrupt the chromatographic process, leading to delays, inconsistent results, and potential damage to the system. Pressure-related problems typically arise from malfunctions in the fluidic path, pump components, or system settings. This section focuses on common pressure-related issues, such as no pressure display or unstable pressure, and provides practical guidance to address them effectively.
No Pressure Display and No Flow of Mobile Phase
1. Power Issues
Cause: The power supply is disconnected, or the HPLC system is not turned on.
Solution: Ensure the power cable is securely connected to the outlet; Turn on the HPLC system and verify proper startup.
2. Blown Fuse
Cause: A fuse in the power supply has burned out.
Solution: Replace the damaged fuse with a new one, ensuring it matches the specifications of the system.
3. Controller Settings Incorrect or Failed
Cause: The pump controller settings are incorrect, or the controller has malfunctioned.
Solution: Adjust the controller to the correct settings for the desired flow rate and pressure. If the controller is defective, repair or replace it.
4. Broken Plunger Rod
Cause: The plunger rod within the pump is damaged or broken.
Solution: Replace the broken plunger rod with a new one.
5. Air in the Pump Head
Cause: Air bubbles have entered the pump head, disrupting the flow of the mobile phase.
Solution: Prime the system by degassing the mobile phase; Use the pump’s purge function to remove trapped air.
6. Insufficient Mobile Phase
Cause: The mobile phase reservoir is empty or too low to maintain proper flow.
Solution: Refill the reservoir with sufficient mobile phase; Check and replace the inlet filter if it is clogged or damaged.
7. Damaged Check Valve
Cause: A check valve in the pump is damaged, causing a failure in maintaining unidirectional flow.
Solution: Replace the damaged check valve to restore proper flow functionality.
8. Leaks in the System
Cause: There are leaks in the fluidic connections, reducing pressure and preventing proper flow.
Solution: Tighten all fittings securely to eliminate leaks; Replace damaged or worn-out seals, connectors, or fittings if necessary.Your Content Goes Here
Sustained High Pressure
1. Flow Rate Set Too High
Cause: The flow rate is set beyond the system’s operational limit, leading to excessive pressure.
Solution: Adjust the flow rate to a level suitable for the column and method being used; Ensure the flow rate adheres to the manufacturer’s recommendations.
2. Blockage in the Pre-Column or Column
Cause: Accumulation of debris, particles, or contaminants in the pre-column or main column creates a restriction in the flow path.
Solution: Reverse flush the column (if allowed by the column’s specifications) to remove blockages; Replace the pre-column if it is clogged; Replace the main column if cleaning does not resolve the issue.
3. Improper Mobile Phase or Precipitation of Solvents
Cause: The mobile phase used is inappropriate or has caused precipitation, leading to blockages in the column.
Solution: Use a mobile phase that is compatible with the method and analytes; Flush the column with suitable solvents to dissolve any precipitated material.
4. Incorrect Column Selection
Cause: The selected column is not suitable for the application, causing excessive resistance to flow.
Solution: Choose a column with appropriate particle size, pore size, and internal diameter for the specific application.
5. Damaged Sample Injection Valve
Cause: The sample injection valve is malfunctioning, leading to restricted flow.
Solution: Clean or replace the sample injection valve as needed.
6. Column Temperature Too Low
Cause: Inadequate column temperature reduces solvent viscosity, increasing pressure in the system.
Solution: Increase the column temperature to the recommended level to reduce solvent viscosity and pressure.
7. Malfunctioning Controller
Cause: The pump controller is not functioning correctly, leading to improper flow regulation.
Solution: Repair or replace the pump controller to ensure proper pressure control.
8. Blocked Guard Column
Cause: The guard column has become clogged with contaminants from the sample or mobile phase.
Solution: Clean or replace the guard column to restore normal flow.
9. Blockage in the Inline Filter
Cause: The inline filter is clogged, restricting flow and causing high pressure.
Solution: Clean or replace the inline filter to remove blockages.
Sustained Low Pressure
1. Flow Rate Set Too Low
Cause: The flow rate is set too low, resulting in insufficient pressure buildup in the system.
Solution: Adjust the flow rate to an appropriate level based on the method and column specifications; Ensure the flow rate matches the recommended operating range for the column to maintain consistent pressure.
2. System Leak
Cause: Leaks in the system, such as at fittings, seals, or tubing, reduce pressure and disrupt the flow of the mobile phase.
Solution: Inspect the system for visible signs of leaks, particularly around fittings, seals, and tubing connections; Identify the exact location of the leak and repair it by tightening fittings or replacing damaged components such as O-rings, seals, or connectors.
Perform regular system maintenance to prevent leaks.
3. Incorrect Column Selection
Cause: The column used has a larger internal diameter, larger particle size, or lower resistance, which results in lower backpressure.
Solution: Select a column that is suitable for the analytical method, ensuring it has the proper internal diameter, particle size, and pore size to generate the required pressure; Use a column with smaller particle sizes or narrower diameters to increase backpressure if appropriate for the analysis.
4. Column Temperature Too High
Cause: Excessive column temperature reduces the viscosity of the mobile phase, which can lower the system pressure.
Solution: Reduce the column temperature to the recommended range for the mobile phase and column; Monitor and stabilize the column temperature to avoid pressure fluctuations caused by inconsistent heating.
5. Malfunctioning Controller
Cause: A defective pump controller may fail to maintain the desired flow rate and pressure.
Solution: Test the functionality of the controller to verify whether it is regulating the flow and pressure correctly; Repair or replace the controller if it is malfunctioning to ensure stable system operation.
6. Partially Blocked Solvent Inlet Filter
Cause: A partially blocked or clogged solvent inlet filter restricts the flow of the mobile phase into the pump.
Solution: Clean or replace the solvent inlet filter to ensure an unobstructed flow of mobile phase.
7. Air in the System
Cause: Air bubbles in the pump or tubing disrupt the flow of the mobile phase, leading to pressure irregularities.
Solution: Prime the system to remove air bubbles from the pump and tubing; Degas the mobile phase before use to minimize the introduction of air into the system.
Pressure Fluctuation
1. Air in the Pump
Cause: Air bubbles trapped in the pump reduce the stability of the flow rate, leading to erratic pressure readings.
Solution:
a. Degas the solvent thoroughly before use to eliminate dissolved gases.
b. Prime the pump to remove any air bubbles already present.
2. Damaged Check Valve
Cause: A malfunctioning or damaged check valve can fail to regulate the direction of flow properly, causing pressure fluctuations.
Solution: Replace the damaged check valve with a new one to restore normal system function.
3. Worn Pump Seals
Cause: Degraded or worn pump seals result in inconsistent delivery of the mobile phase, causing pressure instability.
Solution: Replace the pump seals to ensure consistent and accurate flow delivery.
4. Inadequate Degassing of Solvent
Cause: Insufficient degassing of the mobile phase can allow air bubbles to form in the system, contributing to pressure fluctuations.
Solution:
a. Degas the solvent more thoroughly using vacuum filtration, sonication, or sparging.
b. Consider using an online degassing system for continuous and effective degassing.
5. System Leakage
Cause: Leaks in the system, such as at fittings or seals, disrupt the flow of the mobile phase and lead to inconsistent pressure.
Solution: Inspect the system for leaks, identify the location, and repair it by tightening or replacing damaged components.
6. Use of Gradient Elution
Cause: Gradient elution can cause pressure fluctuations due to changes in the viscosity of the mobile phase as the composition varies.
Solution: Be aware that minor pressure fluctuations during gradient elution are normal and unavoidable; Optimize the gradient profile to minimize abrupt changes in mobile phase viscosity.
7. Partially Clogged Solvent Inlet Filter
Cause: A partially clogged solvent inlet filter restricts the flow of the mobile phase, causing pressure irregularities.
Solution: Clean or replace the solvent inlet filter to restore an unobstructed flow.
No Pressure Display Despite Normal Mobile Phase Flow
1. Faulty Instrument Display
Cause: A malfunctioning instrument display or control unit fails to show the pressure reading correctly, even though the pressure in the system is normal.
Solution: Replace the instrument or repair the display panel to restore proper functionality.
2. Damaged Pressure Sensor
Cause: A defective pressure sensor is unable to measure or transmit the pressure reading to the system display, leading to a false zero-pressure reading.
Solution: Replace the faulty pressure sensor with a new one to ensure accurate pressure detection and display.
In addition, you can also try the following operations to solve the problem.
System Diagnostics: Conduct system diagnostics to confirm that the issue lies with the pressure sensor or display unit and not other system components.
Error Log Check: Review the system’s error logs (if available) to identify potential errors related to sensor communication or instrument malfunctions.
Leakage Issues
Leaks are a common problem, but if not addressed promptly they can severely impact performance, cause contamination, and lead to system damage. This can usually be solved by tightening or replacing the pipe fittings, but it is important to note that over-tightening can cause leakage in metal fittings and wear in plastic fittings. Below, we explore specific leakage scenarios, their causes, and practical solutions.
Leakage at Fittings
1. Loose Fitting
Cause: The fitting is not tightened sufficiently, leading to a gap that allows mobile phase leakage.
Solution: Tighten the fitting securely, ensuring it is snug but not overtightened to avoid damage.
2. Damaged or Worn Fitting
Cause: Prolonged use or improper handling may lead to wear or physical damage to the fitting, making it unable to seal properly.
Solution: Replace the damaged or worn fitting with a new one to ensure a proper seal.
3. Overtightened Fitting
Cause: Excessive tightening of the fitting can deform the sealing surface, compromising its ability to maintain a proper seal.
Solution:
a. Loosen the fitting and retighten it properly, avoiding excessive force.
b. If the fitting is permanently damaged, replace it with a new one.
4. Contaminated Fitting or Connection Surface
Cause: Dirt, debris, or chemical residues on the fitting or its connection surface can prevent a proper seal.
Solution:
a. Disassemble the fitting and clean it thoroughly using an appropriate solvent.
b. Replace the fitting if cleaning does not resolve the issue or if contamination has caused permanent damage.
5. Mismatched Components
Cause: Using fittings and connectors from different brands or models may result in an imperfect fit, leading to leakage.
Solution: Use components from the same brand or ensure compatibility between parts when selecting connectors and fittings.
Leakage at the Injection Valve
1. Damaged Rotor Seal
Cause: The rotor seal, a critical component in the injection valve, can wear out over time or become damaged due to improper handling or high-pressure operation.
Solution: Reinstall the rotor seal properly if it is dislodged. If the seal is damaged or worn out, replace it with a new one to restore proper function.
2. Blocked Sample Loop (Quantitative Loop)
Cause: The sample loop may become obstructed by particulate matter, residue, or crystallized solvents, preventing proper flow and causing pressure buildup or leakage.
Solution: Replace the blocked sample loop with a new one, and ensure proper cleaning protocols are followed to prevent future blockages.
3. Loose Injection Port Seal
Cause: The seal around the injection port may loosen over time, leading to leakage during sample introduction.
Solution: Tighten the injection port seal carefully to ensure it is secure, but avoid overtightening to prevent damage.
4. Incompatible Injection Needle Size
Cause: Using an injection needle with incorrect dimensions can damage the valve or fail to create a proper seal, leading to leakage.
Solution: Use an injection needle of the appropriate size and specifications recommended by the system manufacturer.
5. Siphoning Effect in the Waste Line
Cause: A siphoning effect can occur if the waste line is positioned below the liquid level in the waste container, causing backflow and leakage around the valve.
Solution: Ensure the waste line is positioned above the liquid level in the waste container to prevent siphoning.
6. Blocked Waste Line
Cause: A blocked waste line can impede proper drainage, leading to pressure buildup and leakage around the injection valve.
Solution: Replace or unclog the waste line to restore unobstructed flow of waste liquid.
Pump Leakage
1. Loose Check Valve
Cause: The check valve may become loose over time due to vibrations or improper installation, resulting in leakage.
Solution: Tighten the check valve securely, but avoid overtightening to prevent damage. If tightening does not resolve the issue, replace the check valve with a new one.
2. Loose Fittings
Cause: Loose fittings at the connection points can lead to fluid escaping from the pump.
Solution: Tighten the fittings carefully to ensure a proper seal, but avoid excessive force that could damage the components.
3. Damaged Mixer Seal
Cause: The seal in the mixing chamber may wear out or become damaged, causing leakage.
Solution: Replace the mixer seal or, if necessary, replace the entire mixer assembly to restore functionality.
4. Pump Seal Failure
Cause: The pump seal can degrade due to prolonged use or exposure to harsh solvents, leading to fluid leakage.
Solution: Repair or replace the pump seal with a compatible component designed for the specific solvent used in your system.
5. Pressure Sensor Damage
Cause: A damaged pressure sensor can fail to regulate or withstand the pressure in the system, causing leaks.
Solution: Repair or replace the pressure sensor to ensure proper pressure regulation and eliminate leakage.
6. Damaged Pulse Dampener
Cause: A malfunctioning pulse dampener may lose its ability to smooth out pressure fluctuations, resulting in leakage from the pump.
Solution: Replace the pulse dampener to restore normal operation.
7. Damaged Proportioning Valve
Cause: A malfunctioning proportioning valve, such as a diaphragm rupture or worn components, can lead to fluid leakage.
Solution: Inspect the diaphragm and fittings; if damage is detected, replace the damaged components immediately.
8. Loose or Damaged Purge Valve
Cause: A loose or worn purge valve can fail to maintain a proper seal, resulting in leakage.
Solution: Tighten the purge valve if it is loose, or replace it if it is damaged.
Detector Leakage
1. Damaged Flow Cell Gasket
Cause: The gasket in the flow cell can become worn out or damaged over time, leading to leakage, especially under high background pressure or sudden pressure changes.
Solution:
a. Avoid excessive background pressure or pressure drops that may accelerate gasket wear.
b. Replace the flow cell gasket with a new, compatible one.
2. Broken Flow Cell Window
Cause: The flow cell window may crack or break due to mechanical stress, improper handling, or excessive pressure.
Solution: Replace the flow cell window with a new one, ensuring that it is correctly installed and compatible with the system specifications.
3. Leaking Hand-Tight Fittings
Cause: Hand-tight fittings may loosen during operation or may not have been properly secured, causing leakage at the connection points.
Solution:
a. Tighten the hand-tight fittings securely, ensuring proper alignment and sealing.
b. If tightening does not resolve the issue, replace the fittings with new ones.
4. Blocked Flow Cell
Cause: Blockages in the flow cell can disrupt the flow of the mobile phase, increasing pressure and potentially causing leaks.
Solution:
a. Clean the flow cell to remove any blockages or contaminants.
b. If cleaning does not resolve the issue, reinstall or replace the flow cell as necessary.
Column Leakage
1. Loose End Fittings
Cause: The end fittings of the column may become loose during installation or operation, resulting in leakage at the connection points.
Solution: Tighten the end fittings securely using an appropriate wrench. Be cautious not to overtighten, as this can damage the fitting or column hardware.
2. Particles in the Ferrule
Cause: Particles or packing material from the column may accumulate in the ferrule, preventing a proper seal and causing leaks.
Solution:
a. Disassemble the ferrule carefully.
b. Clean the ferrule and the surrounding components to remove any residual particles.
c. Reinstall the ferrule, ensuring proper alignment and sealing.
3. Inappropriate Sintered Frit Thickness
Cause: The sintered frit at the end of the column may not be of the correct thickness, leading to poor sealing or fluid leakage.
Solution: Replace the sintered frit with one of the correct thickness that is compatible with the column and system requirements.
Sintered Frit Selection Guide
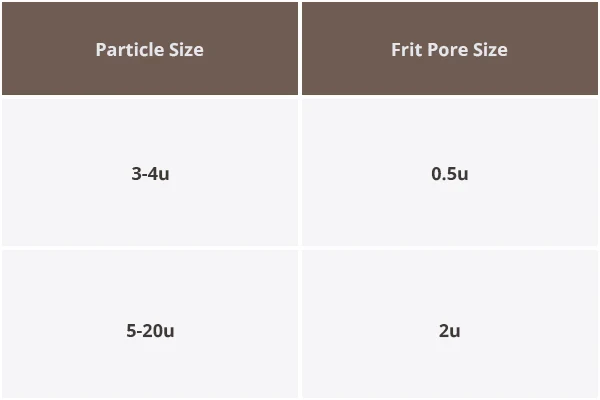
Peak Shape Issues
Peak shape issues are among the most common challenges encountered in HPLC analysis, directly impacting the accuracy and reproducibility of results. Poorly shaped peaks, such as tailing, fronting, or broadening, can arise from various system, method, or sample-related factors.
Identifying and addressing the root causes of these issues is essential to ensure reliable separation, accurate quantification, and consistent performance of the chromatographic system.
The following sections outline the primary causes and solutions for different peak shape abnormalities.
Peak Tailing

1. Blocked Frit
Cause: The frit at the column inlet becomes clogged with particulate matter, restricting flow and causing uneven distribution of the mobile phase.
Solution:
a. Perform reverse flushing of the column to clear the blockage.
b. Replace the inlet frit with a new one.
c. Replace the column entirely if necessary.
2. Collapsed Column Bed
Cause: The packing material inside the column collapses due to excessive backpressure, improper handling, or the use of incompatible solvents.
Solution: Repack the column or replace it with a new column that is properly maintained.
3. Interfering Peaks
Cause: Overlapping peaks or co-eluting compounds in the sample cause distortion of the target peak.
Solution:
a. Use a longer column to improve separation.
b. Optimize the mobile phase composition or replace the column with one better suited to the separation.
4. Improper Mobile Phase pH
Cause: A poorly selected pH for the mobile phase can lead to incomplete ionization of analytes, causing interaction with the column packing material and resulting in peak tailing.
Solution: Adjust the pH of the mobile phase. For basic compounds, a lower pH is often beneficial for achieving symmetrical peaks.
5. Sample-Sorbent Interaction
Cause: Chemical interactions, such as secondary adsorption or solubility issues, occur between the sample and the stationary phase surface.
Solution:
a. Add ion-pairing agents or basic volatile modifiers to the mobile phase to reduce interaction.
b. Switch to a column with a different stationary phase that minimizes sample interactions.
K’ Increase Leads to More Severe Peak Tailing
1. Secondary Retention Effects in Reverse-Phase Mode
Cause: Interaction between analytes and residual silanol groups on the stationary phase, especially with ionizable compounds.
Solution:
a. Add triethylamine (TEA) to the mobile phase to suppress silanol interactions for basic analytes.
b. Add acetic acid for acidic analytes to stabilize their retention.
c. Add salts or buffers to the mobile phase to reduce interactions caused by ionized analytes.
d. Replace the column with one containing end-capped stationary phase or a column with better packing material to minimize secondary retention.
2. Secondary Retention Effects in Normal-Phase Mode
Cause: Adsorption interactions between analytes and the polar stationary phase, which may worsen for compounds with multiple functional groups or strong polar characteristics.
Solution:
a. Add triethylamine (TEA) to the mobile phase for basic analytes.
b. Add acetic acid for acidic analytes.
c. Add water to the mobile phase to reduce polar interactions for multi-functional compounds.
d. Consider switching to an alternative chromatographic method if retention issues persist.
3. Secondary Retention Effects in Ion-Pair Chromatography
Cause: Poor interactions between analytes and ion-pair reagents or inadequate neutralization of stationary phase charges.
Solution:
a. Add triethylamine (TEA) to the mobile phase to stabilize retention of basic analytes and minimize secondary interactions.
b. Optimize the ion-pair reagent concentration and buffer system to improve analyte-stationary phase interactions.
Early Eluting Peaks Exhibit Greater Tailing Than Late Eluting Peaks
1. Column Extraneous Effects (Extra-Column Effects)
Cause: Extra-column effects arise from dead volumes in the HPLC system, including tubing, connections, and the detector flow cell. These effects disproportionately impact early eluting peaks because their narrower peak widths are more sensitive to dispersion and band broadening outside the column.
Solution:
a. Optimize the system configuration by using shorter and narrower tubing to minimize dead volume.
b. Replace the detector’s flow cell with a smaller-volume flow cell to reduce extra-column dispersion.
Tailing of Peaks for Acidic or Basic Compounds
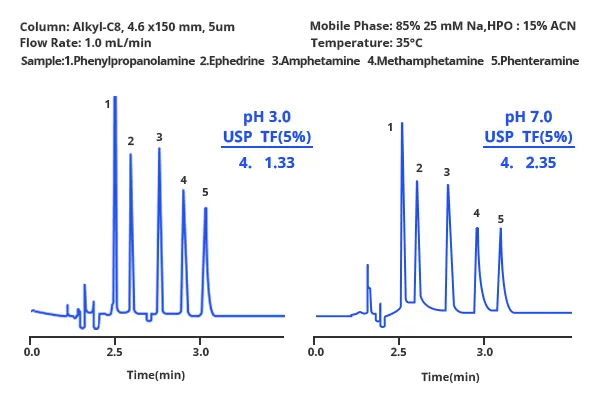
1. Inappropriate Buffering
Cause: Peak tailing for acidic or basic compounds often arises due to improper buffering in the mobile phase. If the buffer concentration is too low or its pKa does not match the pH of the mobile phase, it can lead to inadequate ion suppression or poor ionization control of analytes. This results in secondary interactions between the analytes and the stationary phase, causing asymmetric peak shapes. Such issues are common in reverse-phase chromatography when dealing with weak acids or bases.
Solution:
a. Use a buffer concentration of 50–100 mM to ensure sufficient buffering capacity. This minimizes pH fluctuations and stabilizes the ionization state of the analytes, reducing tailing.
b. Select a buffer with a pKa close to the pH of the mobile phase to optimize ionization control. For example, phosphate buffers are effective in pH ranges of 2.5–7.5, while ammonium acetate or ammonium formate is suitable for pH ranges around 4–6.
c. Fine-tune the pH of the mobile phase to ensure that the analyte remains in its neutral or properly ionized state, depending on the separation goal. For acidic compounds, this may mean adjusting the pH below their pKa, and for basic compounds, adjusting it above their pKa.
Peak Deformation
1. Sample Overloading
Cause: Peak deformation often occurs when the injected sample quantity exceeds the capacity of the stationary phase. In reverse-phase HPLC, this can result in broad, distorted peaks due to insufficient interaction between the sample and the stationary phase. Overloading affects both analytical and preparative separations, reducing resolution and accuracy.
Solution:
a. Reduce the sample load to a level within the capacity of the column. This ensures proper interaction with the stationary phase and minimizes peak distortion.
b. For high-concentration samples, consider using a larger-capacity column designed for preparative chromatography or diluting the sample prior to injection.
c. Optimize the injection volume and concentration based on the specific column’s load tolerance, as provided in the manufacturer’s specifications.
Deformation of Early Eluting Peaks
1. Inappropriate Sample Solvent
Cause: Early eluting peaks are particularly sensitive to solvent effects because they spend less time on the column and are more influenced by initial dispersion at the column inlet. When the sample solvent has a significantly higher polarity or organic content compared to the mobile phase, it can disrupt sample focusing, resulting in broadened, distorted peaks for early eluting compounds.
Solution:
a. Reduce the injection volume to limit the amount of incompatible solvent introduced to the system, minimizing its impact on peak shape.
b. Use a low-polarity solvent that is more compatible with the mobile phase composition. For instance, in reverse-phase HPLC, prepare the sample in a solvent with a polarity closer to the initial mobile phase conditions, such as water or a low-percentage organic mixture.
c. If possible, employ a gradient method that starts with conditions matching the sample solvent to allow better peak formation.
Peak Fronting

1. Low Column Temperature
Cause: A low column temperature can result in incomplete analyte partitioning between the stationary and mobile phases, leading to peak fronting.
Solution: Increase the column temperature to optimize analyte interaction and improve peak shape.
2. Inappropriate Sample Solvent
Cause: Using a sample solvent with different polarity or viscosity than the mobile phase can disrupt chromatographic equilibrium and cause peak distortion.
Solution: Use the mobile phase as the sample solvent to ensure compatibility and minimize peak fronting.
3. Sample Overloading
Cause: Injecting too much sample can saturate the stationary phase, leading to uneven distribution and fronting peaks.
Solution: Reduce the sample injection volume or concentration to maintain optimal chromatographic performance.
4. Damaged Column
Cause: A damaged column, such as one with blocked frits, uneven packing, or degraded stationary phase, can cause irregular flow and peak fronting.
Solution:
a. Backflush the column to clear blockages.
b. Replace the frit or damaged column components.
c. Repack or replace the column if necessary.
Peak Splitting
1. Contaminated Guard or Analytical Column
Cause: Contamination of the guard or analytical column by retained impurities can disrupt analyte separation and lead to peak splitting.
Solution:
Remove the guard column and reanalyze the sample. Replace the guard column if necessary.
If the analytical column is blocked, clean it using appropriate regeneration protocols.
If contamination persists, check for inlet blockage and replace the frit or the column.
2. Sample Solvent Incompatibility
Cause: A sample solvent that is immiscible or incompatible with the mobile phase can disrupt the chromatographic process, resulting in peak splitting.
Solution: Adjust the sample solvent to match the mobile phase as closely as possible, or use the mobile phase as the sample solvent to ensure compatibility.
Extra Peaks
1. Presence of Additional Components in the Sample
Cause: The sample contains unexpected or unidentified compounds that are being separated during the analysis.
Solution: This is a normal occurrence. Analyze the sample composition to identify the additional components.
2. Carryover Peaks from Previous Injection
Cause: Residual compounds from a previous injection may not have been completely eluted.
Solution:
Increase the run time or adjust the gradient slope to ensure complete elution of all compounds.
Increase the flow rate if appropriate for faster elution.
3. Baseline Disturbances or Ghost Peaks
Cause: Impurities in the mobile phase, incompatible sample solvent, or excessive sample volume can result in ghost peaks.
Solution:
Check the purity of the mobile phase and replace it if contamination is detected.
Use the mobile phase as the sample solvent to ensure compatibility.
Reduce the sample injection volume if necessary.
Broad Peaks
1. Changes in Mobile Phase Composition
Cause: Variations in the mobile phase composition can lead to broad peaks.
Solution: Prepare a fresh batch of mobile phase to ensure consistency.
2. Low Mobile Phase Flow Rate
Cause: Insufficient flow rate may cause diffusion and peak broadening.
Solution: Adjust the flow rate to an appropriate level to prevent peak broadening.
3. Leakage Between Column and Detector
Cause: Leaks in the connection between the column and detector can affect peak shape.
Solution: Check for loose fittings, leaks, or salt buildup. Tighten or replace seals as necessary.
Incorrect Detector Settings
Cause: Suboptimal detector settings may distort peak shapes.
Solution: Verify and adjust the detector settings to optimal parameters.
4. Extra-Column Effects
Cause: Factors outside the column, such as long tubing, large detector flow cells, or large injection volumes, can lead to broad peaks.
Solution:
Reduce the injection volume or dilute the sample to avoid overloading the column.
Shorten tubing and use narrow inner-diameter tubing (0.007–0.01 inches).
Minimize mixing volumes and reduce the response time constant.
5. Low Buffer Concentration
Cause: Insufficient buffer concentration can lead to poor peak shape and excessive band broadening.
Solution: Increase the buffer concentration to stabilize peak shape.
6. Contaminated or Ineffective Guard Column
Cause: A fouled or degraded guard column may affect separation efficiency and result in broad peaks.
Solution: Replace or clean the guard column to restore performance.
7. Contaminated Analytical Column or Degraded Stationary Phase
Cause: A polluted analytical column or a degraded stationary phase can reduce column efficiency, causing broad peaks.
Solution: Replace the analytical column. If applicable, clean the column using regeneration techniques.
8. Void Formation at the Column Inlet
Cause: A void at the column inlet disrupts flow uniformity and broadens peaks.
Solution: Open the column, fill the void with packing material, or replace the column entirely.
9. Poor Separation Between Overlapping Peaks
Cause: Peaks that are not fully resolved may appear broad.
Solution: Choose a column with better separation efficiency to improve resolution.
10. Low Column Temperature
Cause: Operating the column at low temperatures can reduce separation efficiency and broaden peaks.
Solution: Increase the column temperature, ensuring it remains within the maximum allowable limit.
11. Excessive Detector Time Constants
Cause: Large time constants in the detector settings can smooth and broaden peaks.
Solution: Use smaller time constants to improve peak resolution and reduce broadening.
All Peaks Have Very Small Areas
1. High Detector Attenuation Setting
Cause: The detector’s attenuation setting is too high, reducing the signal intensity.
Solution: Decrease the attenuation setting to amplify the signal and improve peak area.
2. Large Detector Time Constant
Cause: An excessively large time constant smooths the signal and reduces peak area.
Solution: Use a smaller time constant to enhance signal sensitivity and preserve peak area.
3. Insufficient Sample Injection Volume
Cause: A small injection volume leads to low analyte concentration, resulting in small peak areas.
Solution: Increase the injection volume while ensuring it does not exceed the column’s capacity.
4. Improper Recorder or Data System Connection
Cause: Incorrect connections between the detector and data acquisition system can cause signal loss.
Solution: Verify and use the correct connections to ensure proper data recording.
All Peaks Have Very Large Areas
1. Low Detector Attenuation Setting
Cause: The detector’s attenuation setting is too low, causing the signal to become excessively amplified.
Solution: Increase the attenuation setting to appropriately scale the signal and reduce peak areas.
2. Excessive Sample Injection Volume
Cause: Overloading the column with a large sample injection volume results in exaggerated peak areas.
Solution: Decrease the injection volume to ensure it aligns with the column’s capacity.
3. Improper Recorder or Data System Connection
Cause: Incorrect connections between the detector and the data acquisition system may cause signal misrepresentation.
Solution: Check and ensure proper connections to accurately record the signal.
Baseline Issues
Fluctuations or irregularities in the baseline can compromise data quality and make it challenging to quantify analytes accurately. Common baseline issues, such as baseline drift, noise, or instability, often arise from a variety of factors, including equipment conditions, mobile phase properties, and operational settings. Identifying the root cause is essential to implementing effective solutions and ensuring consistent performance in chroma-tographic analysis.
Baseline Drift
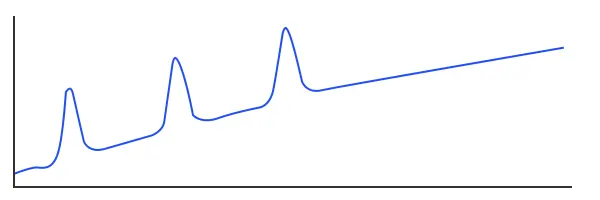
1. Column Temperature Fluctuations
Cause: Even minor temperature changes can lead to baseline drift, especially affecting detectors such as refractive index, conductivity, and lower-sensitivity UV or other photometric detectors.
Solution: Maintain a stable column and mobile phase temperature. Use a heat exchanger before the detector if necessary.
2. Non-Homogeneous Mobile Phase
Cause: Variations in mobile phase composition cause more significant baseline drift than temperature fluctuations.
Solution: Prepare the mobile phase using HPLC-grade solvents, high-purity salts, and additives. Degas the mobile phase before use and sparge with helium during operation.
3. Contaminated or Gas-Filled Flow Cell
Cause: A contaminated flow cell or trapped gas can cause baseline instability.
Solution: Flush the flow cell with methanol or another strong polar solvent. If required, clean with 1N nitric acid (avoid hydrochloric acid).
4. Blocked Detector Outlet
Cause: Blockages at the detector outlet can result in high backpressure, leading to flow cell damage and noisy baselines.
Solution: Remove the obstruction or replace tubing as needed. Refer to the detector manual for flow cell maintenance or window replacement.
5. Improper Mobile Phase Ratio or Flow Rate
Cause: Variations in mobile phase ratio or flow rate can cause baseline drift.
Solution: Regularly check and adjust the mobile phase composition and flow rate. Change the ratio or flow rate as needed.
6. Slow Column Equilibration
Cause: Insufficient equilibration time after a mobile phase change can result in baseline drift.
Solution: Flush the column with 10-20 column volumes of the new mobile phase before analysis.
7. Contaminated or Degraded Mobile Phase
Cause: Poor-quality solvents or contaminated mobile phases can result in baseline instability.
Solution: Use high-quality chemical reagents and HPLC-grade solvents. Check and replace contaminated or degraded mobile phases.
8. Strongly Retained Compounds in the Sample
Cause: Strongly retained compounds (high k’ values) can elute as broad peaks, causing a gradually rising baseline.
Solution: Use a guard column and periodically flush the analytical column with strong solvents during or between injections.
9. Recycled Solvent Without Detector Adjustment
Cause: Using recycled solvent without adjusting the detector can lead to baseline drift.
Solution: Recalibrate the baseline and use fresh mobile phase if the detector’s dynamic range has changed.
10. Incorrect Wavelength Setting
Cause: The detector is not set at the compound’s maximum absorption wavelength, reducing sensitivity and causing baseline fluctuations.
Solution: Adjust the detector wavelength to the maximum absorption wavelength of the analyte.
Baseline Noise (Regular)
1. Air in the Mobile Phase or Detector Flow Cell
Cause: Air bubbles in the mobile phase or detector flow cell can lead to regular baseline noise.
Solution: Degas the mobile phase thoroughly and flush the system to remove air from the detector flow cell.
2. Leaks
Cause: Leaks in the system, especially at tubing connections or seals, can cause irregularities that appear as baseline noise.
Solution: Check all tubing and connections for leaks or loose fittings. Replace seals if necessary to ensure proper system integrity.
3. Incomplete Mixing of Mobile Phase Components
Cause: Poor mixing of mobile phase solvents can lead to fluctuations and noise in the baseline.
Solution: Use proper mixing techniques, such as manual stirring or low-viscosity solvents, to ensure thorough mixing of the mobile phase components.
4. Temperature Fluctuations
Cause: Unstable column or detector temperatures can introduce baseline noise.
Solution: Minimize temperature fluctuations by using a column heater or a thermal jacket to stabilize the system temperature.
5. External Electronic Interference
Cause: Devices on the same electrical line as the HPLC system may cause regular baseline noise.
Solution: Disconnect other devices sharing the same electrical line or improve the system’s grounding to eliminate external interference.
6. Pump Pulsation
Cause: Pressure fluctuations in the pump system can cause periodic baseline noise.
Solution: Use a pulse damper in the system to reduce pump pulsation and stabilize the baseline.
Baseline Noise (Irregular)
1. Leakage
Cause: Leaks at tubing connections or seals can cause irregular baseline noise.
Solution: Inspect all connections and seals for looseness or damage. Replace seals if necessary and check for leaks in the flow cell.
2. Incompatible or Low-Quality Mobile Phase
Cause: The use of low-quality solvents or poorly prepared mobile phases can introduce noise.
Solution: Verify the composition of the mobile phase and ensure that only high-quality solvents and additives are used.
3. Incompatibility Between Mobile Phase and Tubing
Cause: An incompatible mobile phase can result in irregular interactions with the tubing material.
Solution: Select a mobile phase that is compatible with the system’s tubing.
4. Air in the System
Cause: Air bubbles trapped in the system can lead to irregular baseline noise.
Solution: Use degassed solvents to flush the system and remove air bubbles.
5. Detector or Recorder Electronics Issues
Cause: Malfunctions in electronic components of the detector or recorder can produce baseline noise.
Solution: Turn off and restart the detector and recorder, then inspect for electronic faults and correct them as needed.
6. Air in the Detector
Cause: Air bubbles inside the detector can interfere with signal stability.
Solution: Flush the detector thoroughly and install a backpressure regulator after the detector to prevent bubble formation.
7. Contamination in the Flow Cell
Cause: Even trace levels of contaminants can cause noise in the flow cell.
Solution: Clean the flow cell with a 1N acid solution (avoid hydrochloric acid) to remove any impurities.
8. Insufficient Detector Light Source
Cause: A weakened light source in the detector may cause noise.
Solution: Replace the detector lamp with a new one.
9. Column Packing Material Loss or Blockage
Cause: Loss of packing material or blockages in the column can disturb flow and cause noise.
Solution: Replace the column to restore normal operation.
10. Malfunctioning or Improperly Maintained Mixer
Cause: Problems with the mixer or poor maintenance can result in irregular mixing, leading to noise.
Solution: Maintain or replace the mixer. Avoid using a non-dedicated mixing device in the system.
Conclusion
Above we have discussed the common HPLC pressure anomalies, leakage, peak shape and baseline problems and their corresponding solutions. We hope that these contents can provide you with reference in your HPLC experiments and help you obtain accurate and reliable chromatographic results.
At GenFollower, we specialize in providing high-quality laboratory plastic consumables, including filters and other basic products designed to support your HPLC experiments. We welcome you to visit our website and explore our extensive range of laboratory consumables. If you have any questions or specific requirements, please feel free to contact us. Our team will wholeheartedly help you find the right product for your needs. We look forward to serving you!
Recent Posts
Steps for sorting and processing laboratory plastic waste
Laboratories around the world generate a significant amount of plastic waste every day. According to a 2015 study published in Nature, scientific research labs produce over 5.5 million tons of plastic waste annually, with [...]
Ultimate Guide to Robotic Pipette Tips 2025
In the realm of laboratory science, where reproducibility and exactitude define success, precision instruments play a mission-critical role. Among these, pipetting systems stand as indispensable pillars of accurate liquid handling. As laboratories increasingly adopt [...]
Step-by-Step ELISA Protocol: A Comprehensive Guide
What is ELISA? ELISA (Enzyme-Linked Immunosorbent Assay) is a widely used laboratory technique designed to detect and quantify specific soluble molecules — such as proteins, peptides, antibodies, hormones, and biomarkers (e.g., cytokines, chemokines, immunoglobulins) — [...]